The City of New Orleans transforms their emergency response with real-time visibility
The City uses Samsara to manage vehicles and assets across 41 departments, including their Emergency Medical Services and Equipment and Maintenance Division, improving how they track and allocate resources to better serve the public.
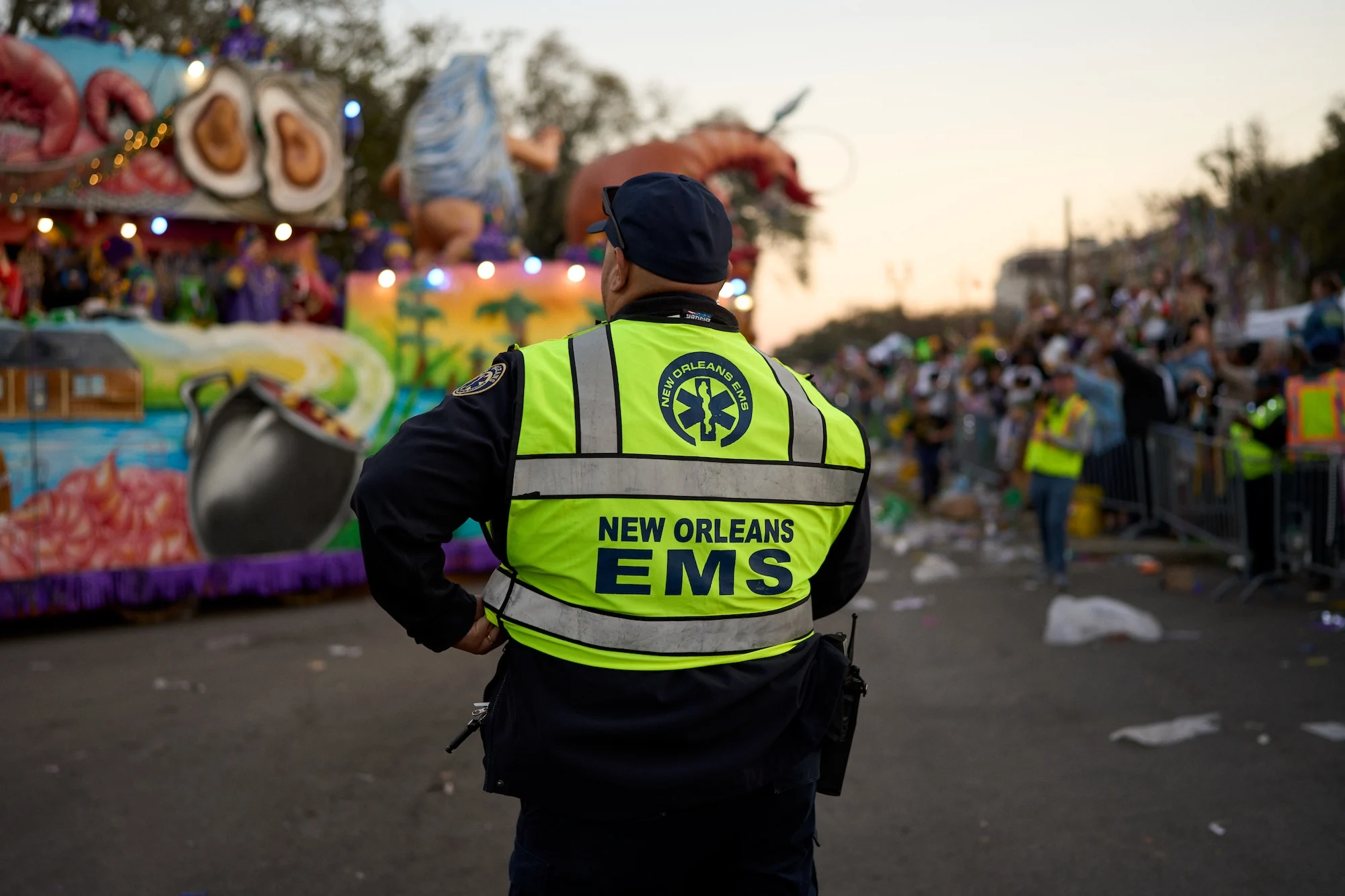
Powered by the Samsara Connected Operations™ Platform
Meet the City of New Orleans
New Orleans EMS needed one solution to track vehicles and assets
The City of New Orleans is a vibrant city located in southeastern Louisiana. Often called "the Big Easy," the city has almost 400,000 residents and welcomes millions of visitors each year for a variety of cultural events, including its most famous celebration, Mardi Gras.
New Orleans is also home to thousands of public servants—including the New Orleans Emergency Medical Services (NOEMS) department—who are dedicated to keeping the City safe. NOEMS relies on a large fleet of ambulances, sprint cars, bicycles, and other vehicles to respond to nearly 70,000 emergency calls every year, as well as provide services during high-profile events like Mardi Gras.
However, a lack of real-time visibility into their vehicles and assets was making it difficult for NOEMS to coordinate emergency response as safely and effectively as possible. "We were using a bunch of different tools, including radio GPS, modem GPS, Apple Air Tags—we were even moving pins around on magnetic boards to try and track our assets,” said Bill Salmeron, Chief of NOEMS. "We needed an updated way to bring everything into one platform to improve how we were operating."
The City began the search for a technology partner that would not only give NOEMS real-time data into asset location to help improve emergency response, but also enhance vehicle maintenance, fuel management, and the safety of providers overall, whether during a busy event like Mardi Gras, or any day of the year.
Gerry Figueroa
A flexible, easy-to-use solution that provides visibility across departments
To modernize their operations, NOEMS implemented Samsara Vehicle Gateways (VGs), AI Dash Cams, and Asset Tags across their fleet. "The main reasons we chose Samsara are because it's a flexible platform that's easy to use," Salmeron said. "Samsara devices were easy to install on many different types of vehicles and assets, and the dashboard and reports are easy to understand."
In addition to NOEMS, Samsara was implemented across 40 City departments, including the Equipment and Maintenance Division (EMD). EMD is responsible for managing a fleet of approximately 2,700 assets—including police, fire, and maintenance vehicles—and they faced similar challenges tracking their fleet. "We really didn’t know where our vehicles were," said Kim DeLarge, Jr., Assistant Chief Administrative Officer. "We would have $450,000 worth of equipment that was just somewhere, and we couldn't easily locate it."
With Samsara VGs, EMD can now see in real time where assets are located and how they're being utilized, helping the City be more transparent and accountable. "Now, we can easily respond to any audit or request for information about any of our vehicles," said Shelita White-Stewart, Chief of Staff-Operations. "We are here to serve our citizens, and Samsara helps us do that more effectively."
AI Dash Cams and driver coaching help providers operate more safely
As part of their overall focus on safety, the City deployed Samsara AI Dash Cams in ambulances and other vehicles to identify unsafe behaviors and to improve coaching for EMTs, paramedics, and other drivers. As a result, NOEMS has been able to reduce speeding by 37% and mobile phone usage by 46% over 12 months, while EMD was able to lower speeding by 16% and collision risk by 81% over six months. The City has also used AI Dash Cams to exonerate drivers and resolve disputes, as well as give providers real-time, turn-by-turn directions to help transport patients to hospitals faster when minutes count.
LEARN HOW

With Vehicle Gateways, the City can proactively maintain their fleet
Samsara telematics data plays a critical role in NOEMS’ ability to deliver fast, effective emergency response. With Samsara VGs, the City can route vehicles to calls more efficiently, as well as help ensure ambulances and other vehicles are up to date on maintenance. "If an ambulance were to break down while transporting a patient, it could be a catastrophic failure," said Palmisano. "With Samsara, we can proactively maintain our fleet and ensure that ambulances and other vehicles are ready when needed."
LEARN HOWSamsara enables the City to track their fleet with one solution
The City uses a wide range of vehicles and assets to respond to emergencies. However, NOEMS had limited visibility into some of their assets, such as bicycles and Special Response Vehicles (SRVs), and they couldn't see all of their vehicles and assets on one map. With Samsara Asset Tag, the City can get real-time location data across their entire fleet, making it faster and easier for commanders to allocate the right assets to the right calls.
LEARN HOW