Powered by the Samsara Connected Operations™ Platform
Meet Hoskins Equipment
Hoskins Equipment needed better visibility to achieve operational excellence across thousands pieces of equipment, dozens of vehicles, and multiple sites
As leaders in high-reach equipment rentals, keeping up with their standard of excellence meant that Hoskins Equipment needed a way to operate more efficiently. Lacking clear visibility into their physical operations, Hoskins sought a solution that would enable them to stretch their resources further so they can work better, faster.
Hoskins saw an opportunity to digitize their processes and take a unified approach to their operations across their drivers, assets, and facilities. At the top of their list was finding an integrated solution that can consolidate these solutions within a single pane of glass—empowering Hoskins to maximize efficiency and centralize their operations.
ALEK JAVIER
Centralized platform transforms their operations
With the Samsara Connected Operations Cloud, Hoskins unified their operations within a single integrated platform. By centralizing data and workstreams across driver safety, asset management, and consolidated video, Hoskins was able to transform their operations—decreasing incidents, reducing costs, and improving back-office efficiency.
Theft mitigation avoids $120K in potential equipment replacement costs
With over 2,600 pieces of equipment, Hoskins faced challenges efficiently tracking their assets, including scissor lifts, boom lifts, forklifts, utility vehicles, and more. The Samsara Asset Tag provides consistent, real-time visibility into asset locations that drastically reduces time spent locating equipment. Moreover, it has played a critical role in preventing theft and loss, saving $120,000 in potential equipment replacement costs within just months of deployment.
Learn more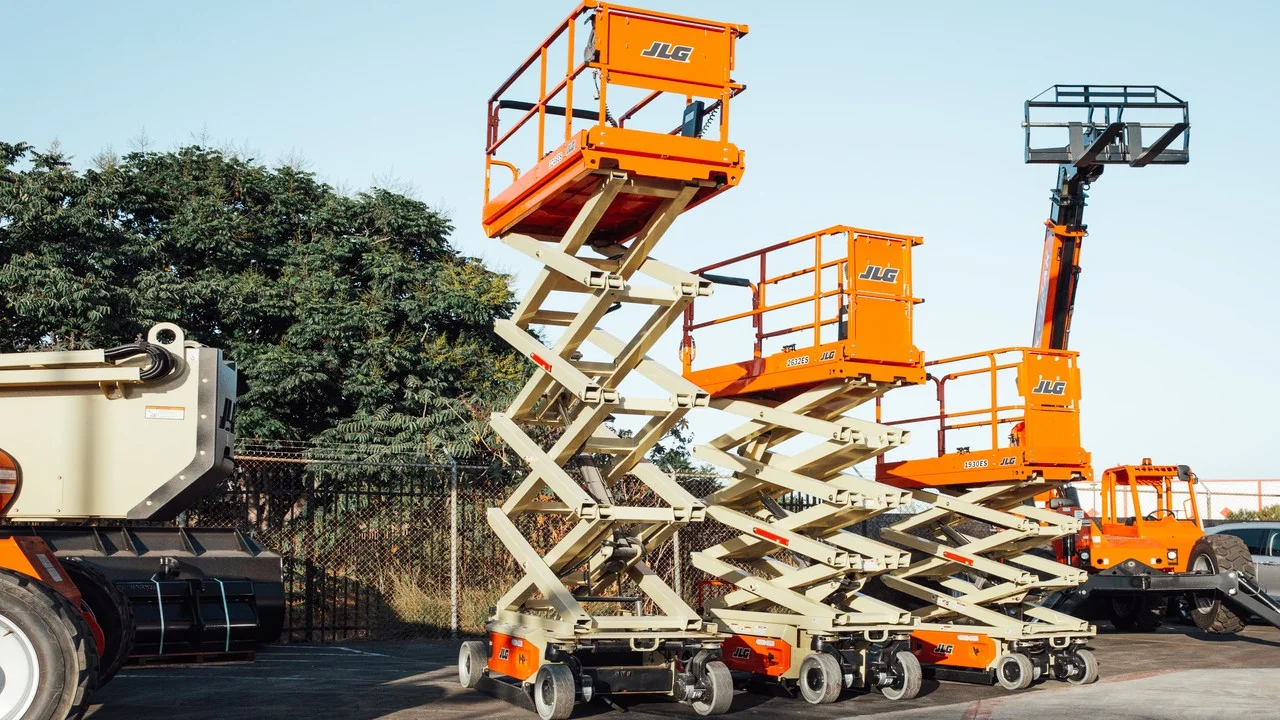

Taking a unified approach to their operations
Hoskins’ previous security camera system was outdated and required tedious, manual review to track down critical video footage. Using Samsara’s integrated platform approach, Hoskins was able to leverage their existing onsite camera infrastructure and consolidate visibility. Now, they can access their vehicle camera streams, camera footage, and asset locations all within a single dashboard.
Learn moreIntelligent Search and AI features accelerate video retrieval
Hoskins no longer needs to manually sift through hours of footage with Site Visibility.
Both IT and line-of-business users can now leverage Samsara’s Intelligent Search and AI features to reduce the time it takes to review footage from a few hours/days to a few minutes per request.
Learn more
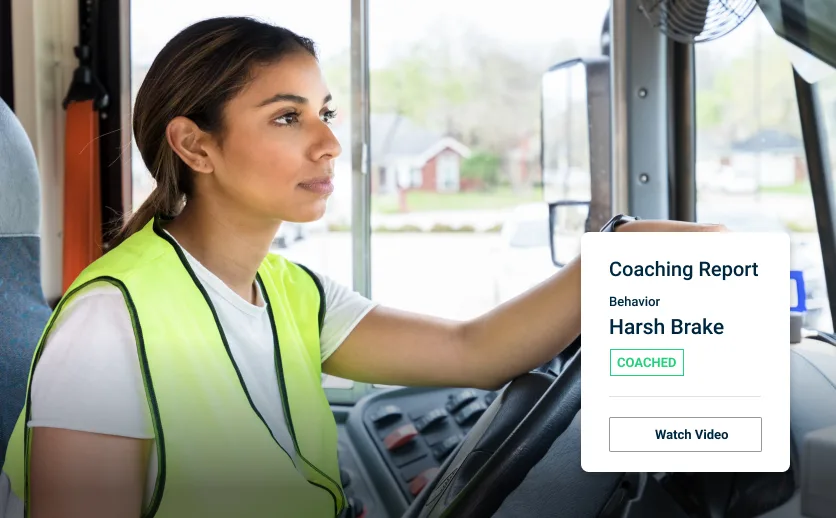
Increased visibility improves driver safety and protects from false blame
With insurance costs rising due to on-the-road incidents, Hoskins needed a way to more effectively identify and coach risky driving behavior. Samsara AI Dash Cams increased visibility across their fleet, improved driver coaching, and decreased incidents. As a result, Hoskins reduced the number of harsh events by 97%.
Learn moreTrack and protect high value assets
Lost or stolen equipment had long troubled the Hoskins team, so they needed a better way to protect their high-value assets. With Samsara Asset Gateways, Hoskins can dynamically track and get full visibility into their equipment fleet as well as other assets in the field. Now, Hoskins is able to recover lost or stolen units and resolve usage disputes with customers, saving them thousands of dollars annually.
“We had consistent issues with lost and stolen equipment that have already started to improve since partnering with Samsara. We’ve used the Asset Gateways to help us find lost units, recover stolen units, and resolve usage disputes with customers.”
Learn more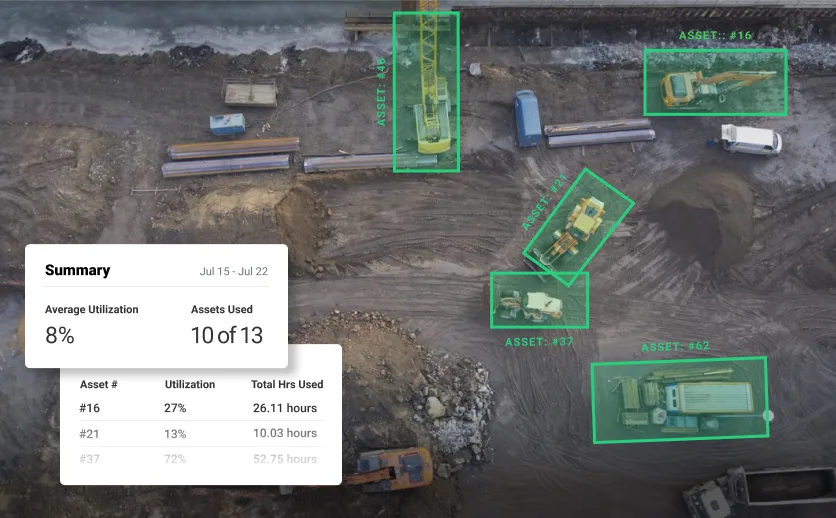