Interstate Waste Services saves $340K+ annually due to efficiency improvements
Interstate Waste Services enhances safety, maximizes efficiency, and drives digital transformation across their operations with the Samsara platform.
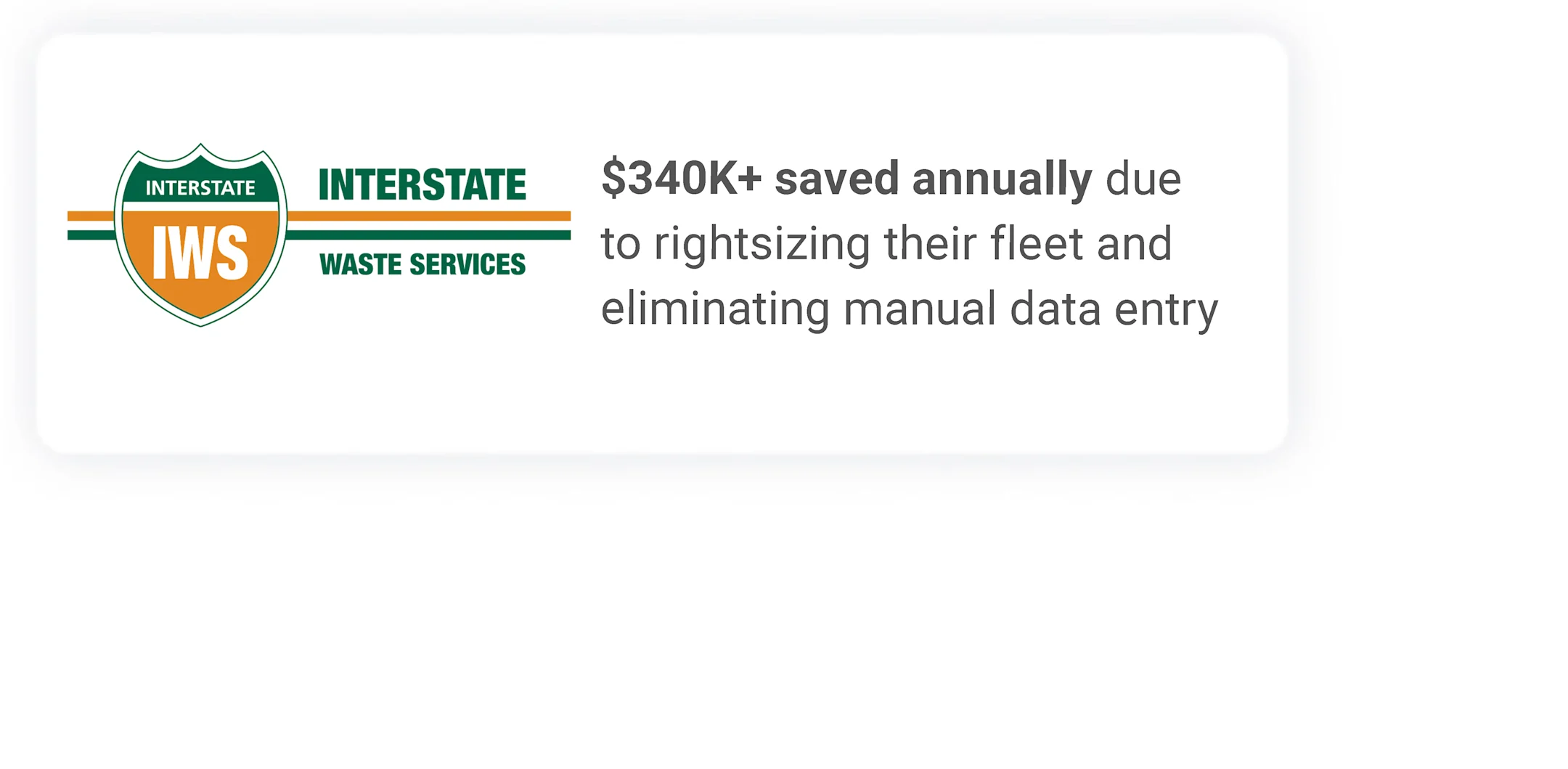
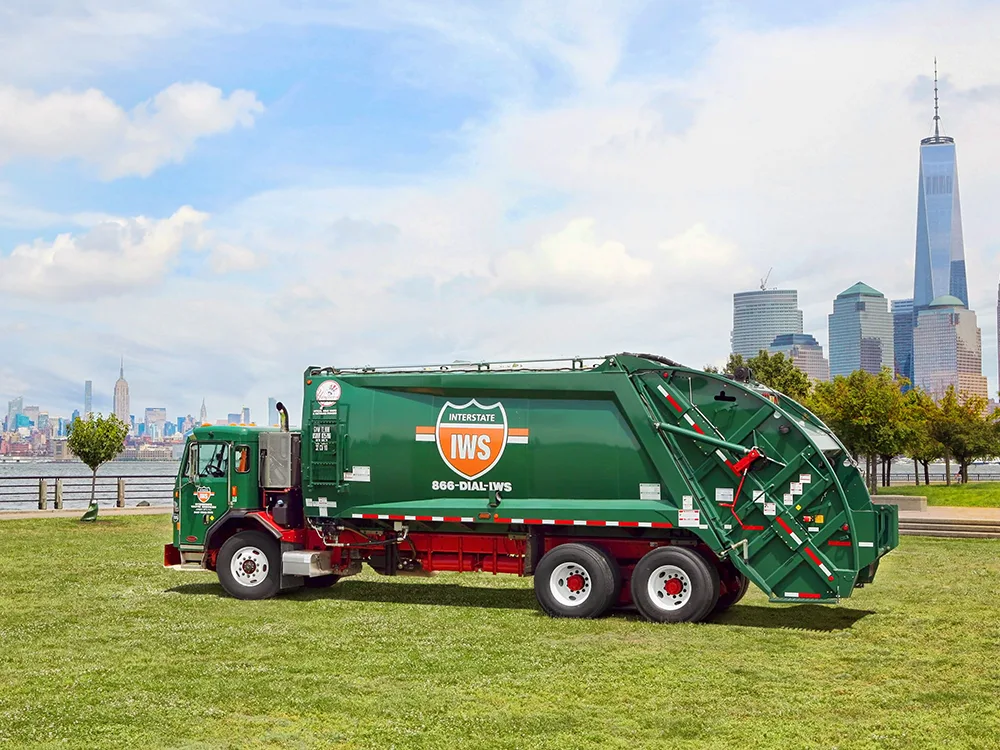
Driving digital transformation on a connected platform.
Meet Interstate Waste Services
Rapid growth and siloed solutions created operational inefficiencies.
Interstate Waste Services (IWS), the largest vertically integrated, privately held waste management company in the U.S., faced operational challenges amid rapid growth. Their previous dash cam vendor struggled to provide reliable footage, making it difficult to review and resolve safety incidents effectively. The IWS team needed high-quality images from side and rear cameras to ensure driver exoneration in no-fault incidents, and AI capabilities to enhance driver safety and coaching. IWS also wanted a comprehensive telematics solution for improved operational efficiency.
To streamline operations, IWS wanted multiple technology solutions connected on a single platform. They sought a partner that could provide robust safety solutions and offer comprehensive telematics, asset tracking, and AI capabilities to support their continued growth.
RAKESH GOPAKUMAR
Innovating together to enhance safety and efficiency.
IWS partnered with Samsara to install AI Dash Cams, Vehicle Telematics, Smart Trailer, and custom API solutions across their operations. The IWS team reduced their installation time by 70% by installing Samsara plug-and-play Dash Cams and Vehicle Gateways in under 15 minutes per vehicle.
These connected solutions provide real-time visibility into their fleet, improving driver safety through in-cab alerts and coaching, streamlining maintenance processes, and enabling efficient asset utilization. As a result, they are able to save thousands of dollars and hours annually, turning their investment in digital transformation into powerful business results.

Enhancing safety with 360-degree visibility and in-cab alerts.
By deploying Samsara AI Dash Cams with HD Camera Connectors, IWS achieved comprehensive, 360-degree visibility in the cab and on the road. In just one year, IWS achieved a 20% reduction in claims costs from intersection collisions due to high-quality dash cam footage and a 15% reduction in coachable incidents after turning on in-cab alerts.
LEARN MORE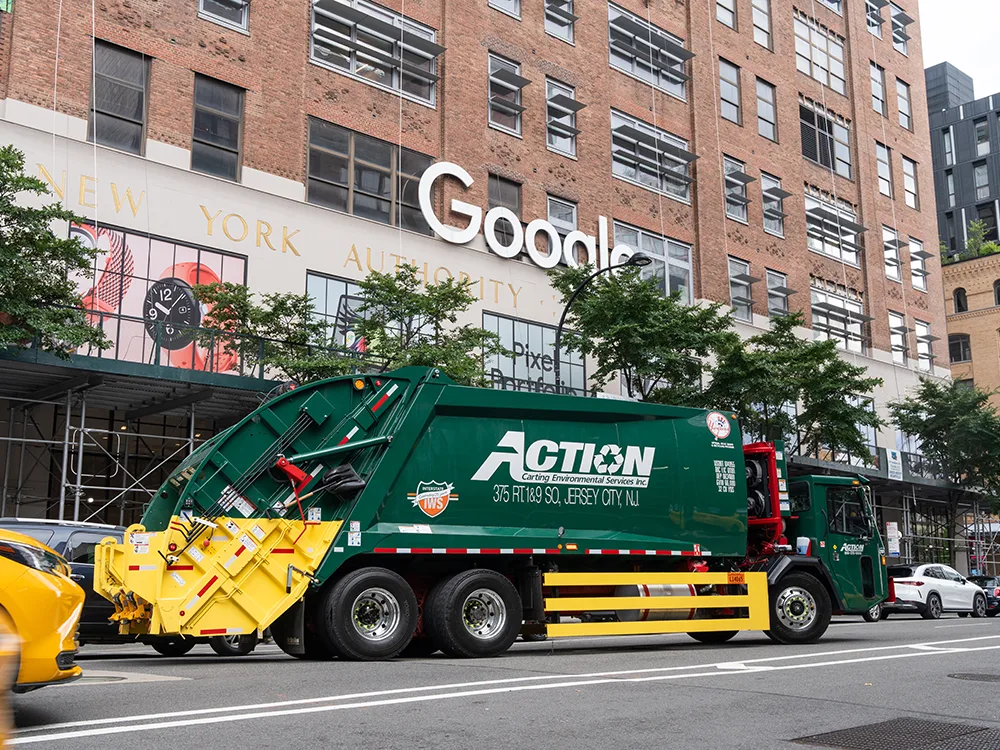
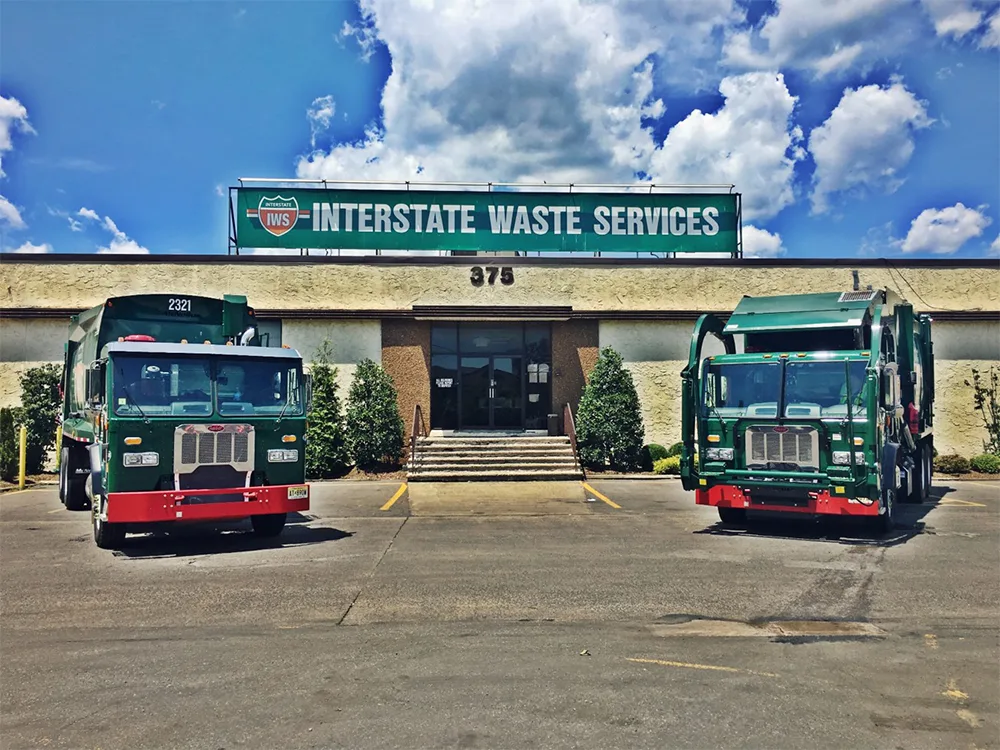
Improving trailer maintenance and utilization.
IWS implemented Samsara’s Smart Trailer solution to enhance the maintenance and utilization of their trailers. By accurately tracking trailer locations and scheduling preventative maintenance, they went from 35% compliant on routine preventive trailer maintenance to 85% compliant, identified and reduced underutilized assets by 21%, and saved $240,000 in one year.
LEARN MOREStreamlining operations with seamless data integration.
IWS leveraged Samsara’s App Marketplace, the largest open ecosystem of partner integrations for physical operations, to integrate their vehicle data seamlessly into their existing maintenance and operational systems. This integration eliminated manual data entry, saving 4,080 hours and $101,000 annually, and ensured accurate and timely driver assignments.
LEARN MORE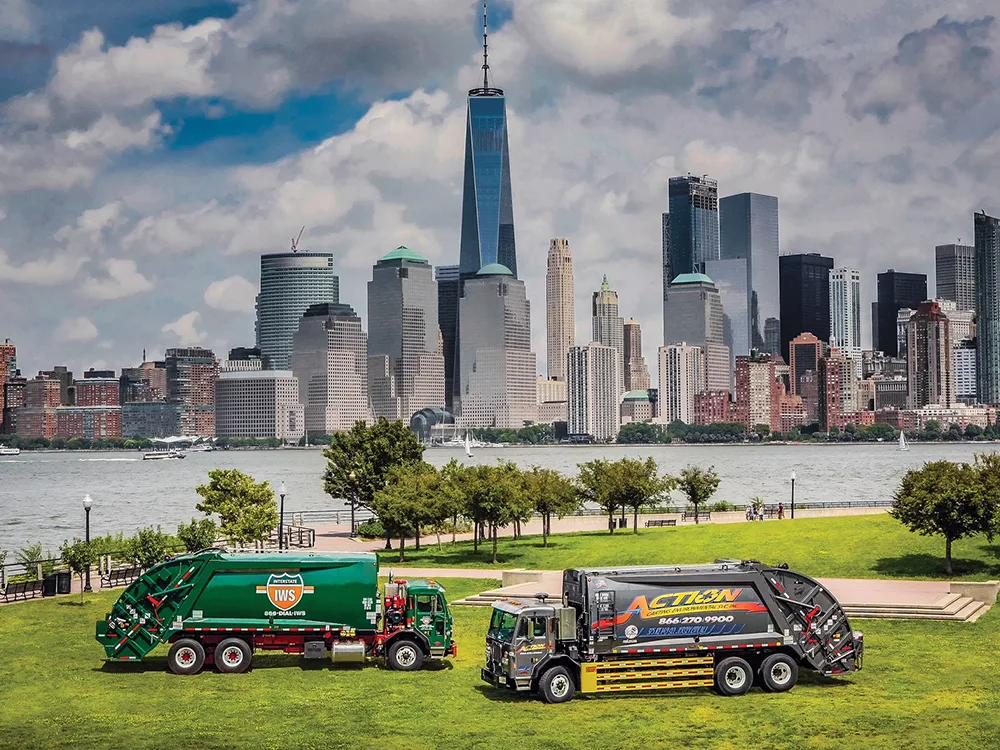
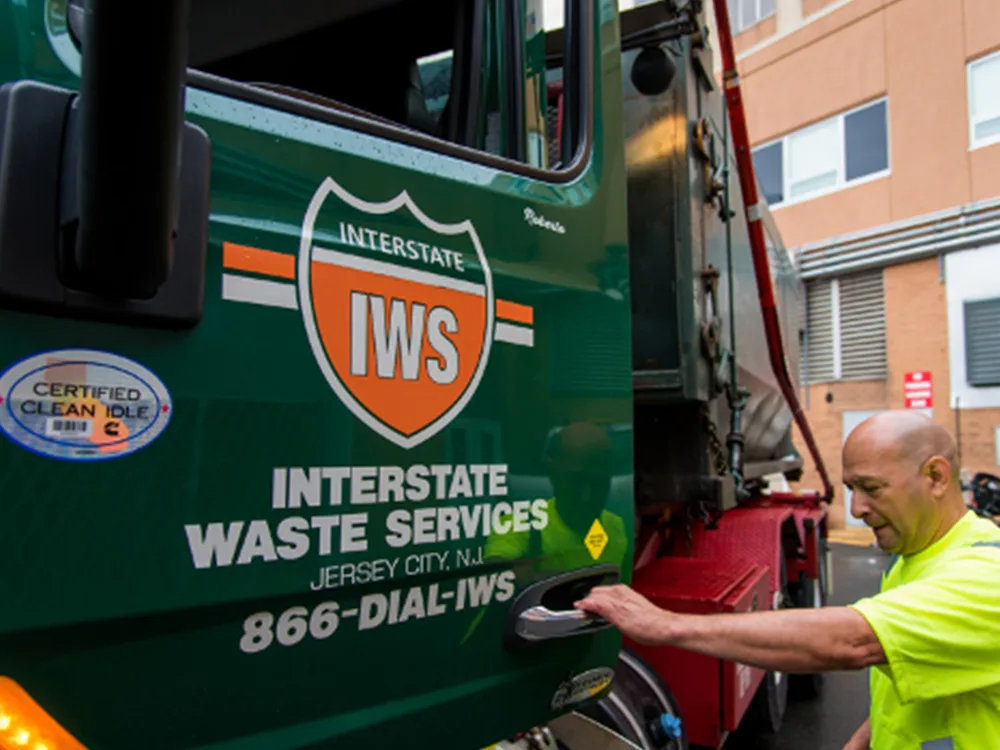
Improving operational visibility with real-time geolocation alerts.
By integrating Samsara Vehicle Telematics into their existing systems, IWS unlocked next-level dispatch efficiency for their short haul operations. The enhanced visibility and GPS insights from Samsara also led to more efficient route planning and reduced fuel consumption.
LEARN MORE