Maxim Crane Works saves $13M with predictive maintenance program
With massive safety and efficiency gains, Maxim’s long-term growth strategy is fueled by their partnership with Samsara.
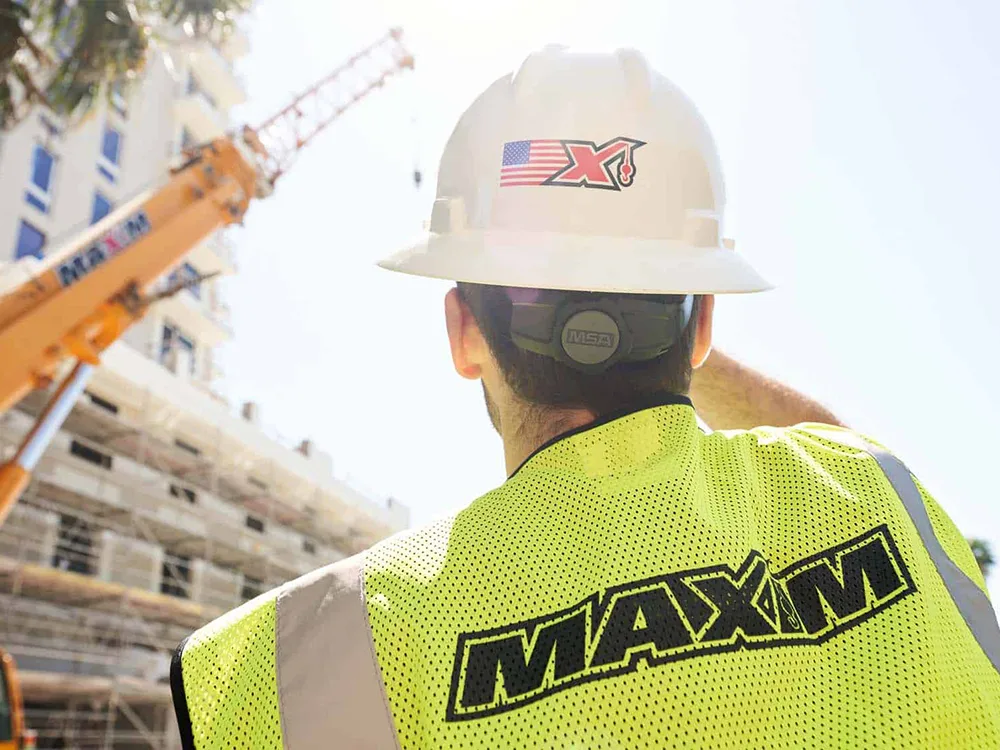
Powered by the Samsara Connected Operations™ Platform
Meet Maxim Crane
Maxim Crane sought a single platform to consolidate operational data and gain valuable insights
Maxim Crane Works (or “Maxim Crane”) is North America’s largest crane rental company and lifting solutions provider serving thousands of customers across 60 locations.
Before Samsara, Maxim Crane had limited visibility into what their employees were experiencing on the road—when accidents occurred, they faced many challenges in verifying what actually happened and proving their employees’ innocence. And, with the largest crane and support fleet in the continental United States, logging tens of millions of on-road miles annually, incidents are inevitable. Additionally, the company’s previous telematics system provided very limited insights. Maxim Crane looked for a solution that could address all of these concerns, in a single, unified platform.
DENNIS COLLINS
A single platform for business transformation that delivers visibility
Maxim Crane chose the Samsara Connected Operations Platform to gain complete visibility across their fleet on one customizable platform. Together, Samsara AI Dash Cams, Fleet Telematics, Asset Tracking, and more provide Maxim Crane with a holistic view into the health of their fleet, how safe their employees are performing, and what’s happening on the road. By embracing real-time data and integrated solutions, Maxim has not only achieved substantial financial savings and efficiency gains but has also cultivated a more proactive and disciplined operational culture.
Safer behavior, fewer incidents, and massive savings
As a result of proactive coaching by AI-powered, in-cab alerts, Maxim Crane improves their most important metric: the safety of their employees. Using AI Dash Cams, they reduced harsh driving events by 94%, speeding by 87% and saved an additional $894,000 in insurance expense reduction with liability claims down 30% from the prior year.
Learn how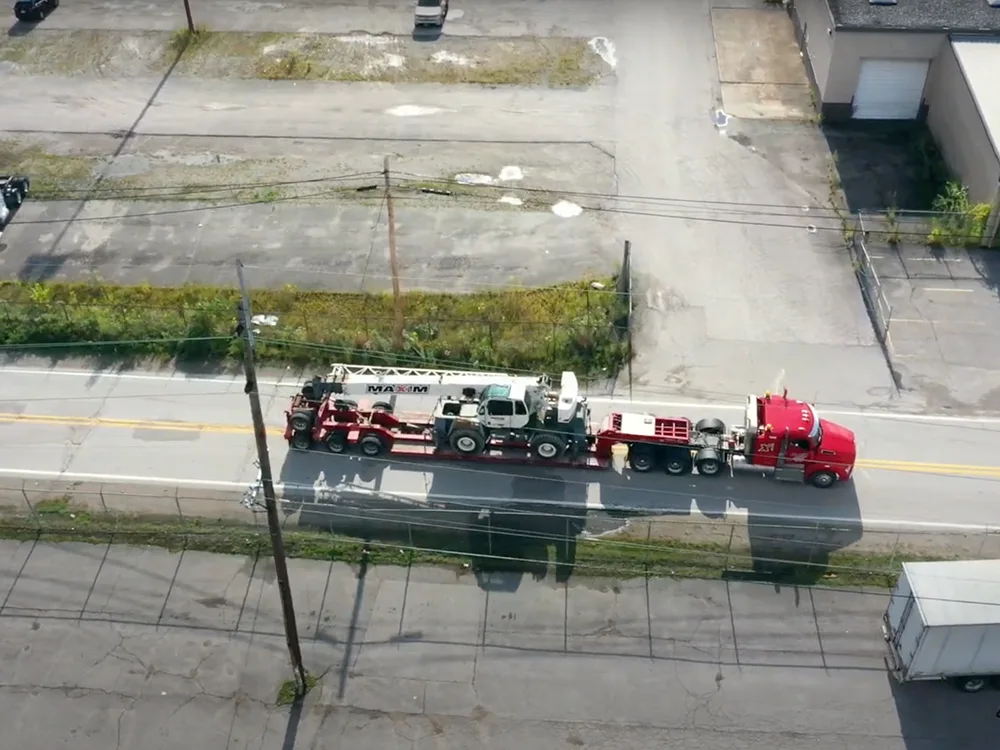
DENNIS COLLINS
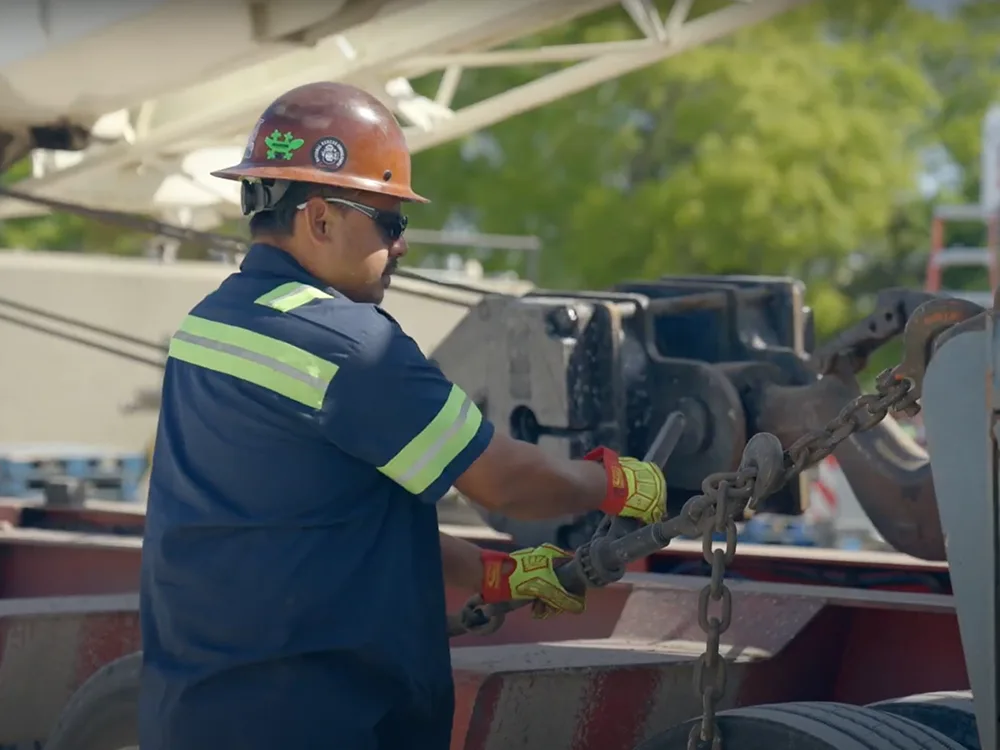
Increased uptime and $13 million saved in maintenance costs
Before Samsara, Maxim Crane’s maintenance program was reactive, meaning they could only address issues once equipment broke down. This often necessitated expensive "hotshot" delivery of parts and weekend overtime for repairs on job sites, leading to increased costs and customer delays. Samsara enabled a shift to a planned, predictive maintenance program, and as a result, they saved approximately $13 million in 2024—about $1 million per month in maintenance costs. Additionally, the precise hours of use data from Samsara allowed Maxim Crane to increase billing for excess equipment usage by 27% year over year, further boosting revenue.
Learn howNext-level efficiency, powered by paperless forms and workflow automation
Before Samsara, Maxim Crane relied on paper forms, which were tedious and inefficient. Now, with Samsara Connected Workflows, they have digitized forms for daily and monthly equipment inspections, equipment delivery and pickup, and even timesheets. This paperless program was a major focus, and they rolled out iPads to 100% of their workforce to support it.
LEARN MORE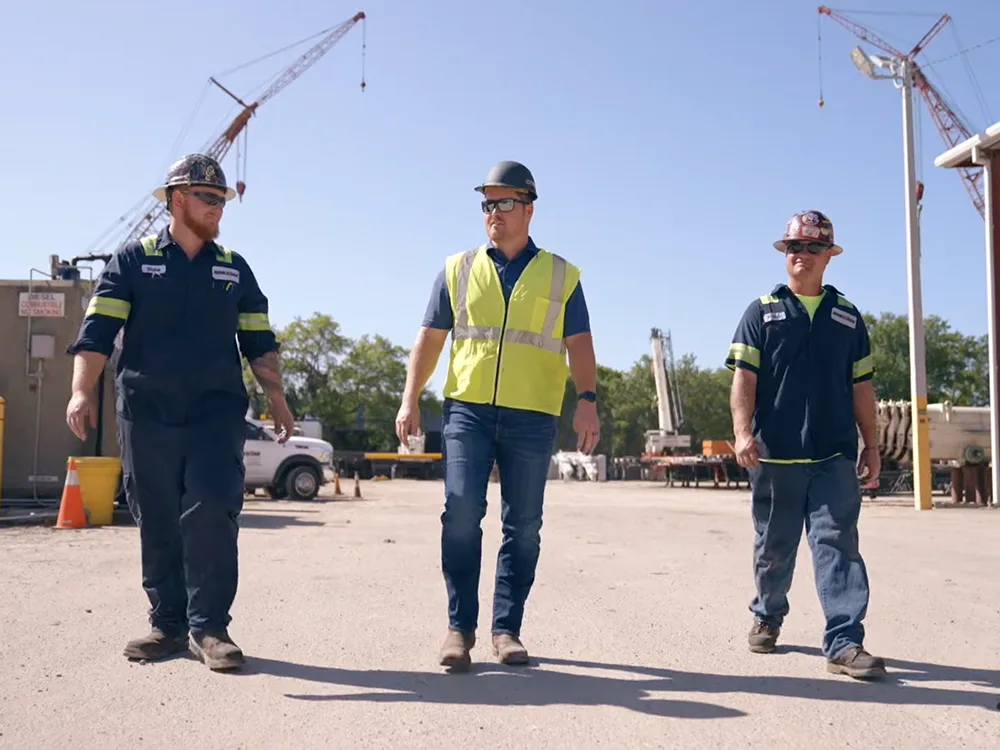